Table of contents
Pneumatics refers to the technique in which mechanical movement is generated with the help of pressurised gas. Like hydraulics, pneumatic systems belong to the field of fluid dynamics. However, whereas pure hydraulics uses liquids as the working material, pneumatics works with compressed air. Plainly put, pneumatics is a simple and reliable way to make things move just by using clean, dry air.
The areas of application are therefore very diverse and using air as a drive medium is also cheap and comparatively environmentally friendly. This is why compressed air and pneumatic tools are so popular.
What does pneumatics mean?
The word pneumatics is derived from the Greek word pneuma, which translated means ‘wind’ or ‘breath’. It refers to a diverse field of technology in which work is carried out with compressed air or compressed air-driven systems.
Pneumatics basics
Pneumatics provides movement and drive, and usually pneumatic cylinders are the first thing associated with this technology. But more specialised and complex systems are also available, such as vacuum systems, grippers or even air springs which are ideal for damping shocks.
Pneumatic systems, also called control systems, work with compressed air. In most systems, this has an overpressure of 6 bar. High-pressure systems, which are used for gas pipelines, work with up to 18 bar. However, the highest pressure needed for the production of products like plastic bottles is up to 40 bar.
How does pneumatics work?
In basic pneumatic systems, air is compressed and fed via valves to the desired location. The energy stored in the compressed air is then converted into kinetic energy and used in specific ways, for example, to move a cylinder piston in a specific direction.
Basically, every pneumatic control system consists of four components:
- Compressed air generation: The required ambient air is drawn in by one or more compressors and then compressed to between 6 and 40 bar depending on requirements. For high air pres-sures that are only needed for a certain period of time, a compressor with speed control is used. Compressing air generates heat that can also be used as a source of heat energy.
- Compressed air treatment: The compressed air is freed from impurities such as dust or pollen using various filter systems. This is important to ensure that the pneumatic systems have the longest possible service life.
- Compressed air distribution: Compressed air is distributed via pipes. To prevent the air from becoming contaminated again, the pipes must be leak-proof and emit as little rust or water as possible. In most cases, storage facilities are also integrated into the pipe networks.
- Application/performance of work: Compressed air is supplied to the respective work process-es via valves or actuators. The number of pneumatic switching positions and connections varies depending on the application and the device. The mechanical work is performed with the help of compressed air by so-called working elements – mainly pneumatic cylinders.
The way in which pneumatic circuits must be constructed is specified for the various systems and devices through corresponding safety standards.
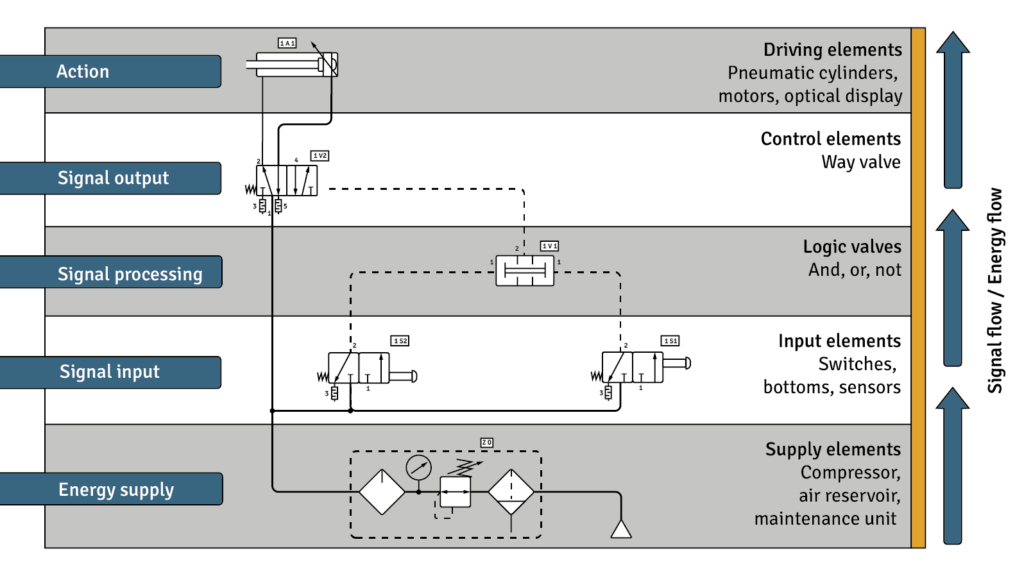
Where is pneumatics used?
Pneumatic systems are used in a wide variety of industries and areas, from hazardous material handling to robotics and medical technology. Other areas of application are drive and transport. For example, systems are installed in air brakes of trucks or buses.
They are also used in air-filled tyres, various lift trucks and other industrial trucks. Pneumatic tube systems can also be used to transport smaller unit loads or liquids. Some special pneumatic tools only work with compressed air – for example in spray painting and other surface treatments.
Advantages of pneumatic systems
Pneumatic systems have several advantages. The source material used, namely air, is environmentally friendly, cheap, and available everywhere. Air can be used in any quantity and can also be transported easily over long distances.
Other advantages of pneumatics are:
- Storage capability: Compressed air can be stored in the appropriate pressure vessels.
- Temperature resistance: Compressed air is insensitive to temperature fluctuations.
- Safety: There is no danger of explosion or fire with compressed air.
- Environmental friendliness: Compressed air that escapes does not cause any environmental damage.
- Simple design: This makes low-cost solutions possible.
- Speed: Compressed air is a very fast working medium.
- Stepless adjustability of forces and speeds: The pressure level can be adjusted to the respective application.
- Force: High forces are possible in a comparatively small installation space.
- Robust against overload
- No additional cooling necessary: The air itself already provides sufficient cooling for the individual drive components.
One of the possible disadvantages of pneumatics is the low level of efficiency. Even if the heat generated during compression is reused, some energy is lost. However, cold temperatures can also become a problem. When compressed air flows through equipment and machines, it can cool them down considerably and can cause ice to build up. Working with pneumatic circuits also generates noise, but this can be reduced by using silencers. It should also be taken into account that the power of compressed air systems is limited.to account that the power of compressed air systems is limited.
FAQs about pneumatics basics
The biggest difference between the two is that pneumatics uses air to generate pressure whereas hydraulics uses oil or water. Since pneumatics does not require a closed system of pipes in which liquids would have to be present, it is usually less complex in structure. Another significant difference between the two principles is so-called compressibility, i.e. the property of either being compressible or not compressible. Gases are compressible, liquids are not. This results in both systems having certain advantages and disadvantages.
Hydraulics can be precisely controlled and can generate very large forces. However, hydraulic oils are expensive and can cause environmental hazards in the event of a leak. Pneumatics is somewhat less precisely controllable due to the compressibility of gases, exhibits heat energy losses, and requires larger cylinder surfaces to generate the force of a smaller hydraulic system. Air is free as well as freely available and not harmful to the environment.
Pneumatics has widespread applications across various industries. It’s commonly used in commercial vehicles for cab, chassis, and engine systems. The energy sector, including oil and gas as well as power generation, relies on pneumatics for various processes. In the food and beverage industry, pneumatics is essential for bottle moulding, automation, and packaging. Manufacturing benefits from pneumatic systems in factory automation, materials handling, and for tasks like gripping, lifting, and sorting. Pneumatics is also used in certain types of factory machinery, such as paint-sprayers. Pneumatic drives perform linear movements and rotating movements. Hence, pneumatics also plays a crucial role in life sciences equipment, rail industry applications such as door control and suspension, and in power tools like road drills, where compressed air is channelled through a pipe to pump a metal chisel into the pavement.
Pneumatic force is not as precisely controllable as hydraulic force. While liquids expand uniformly, gases somewhat cushion the applied pressure. Additionally, there is always some energy loss when air is compressed. During compression, the air heats up. This energy can be used as heating energy. However, if it is not used for this purpose, it is lost.
Moreover, there is a potential danger in this heating, as excessive friction can locally generate such high temperatures that unwanted explosions may occur or heavily loaded components wear out faster. In general, drives of pneumatic systems wear out faster and require regular maintenance. Additionally, pneumatic systems can’t produce as much force as hydraulic systems. This is because hydraulic systems use liquids, which can’t be compressed. These incompressible liquids allow for power to be transferred with very little energy loss, making hydraulic systems more efficient at generating force.
Image source:
© gettyimages.de – Denys Yelmanov